低淬透性冷作模具钢-粉末冶金材料
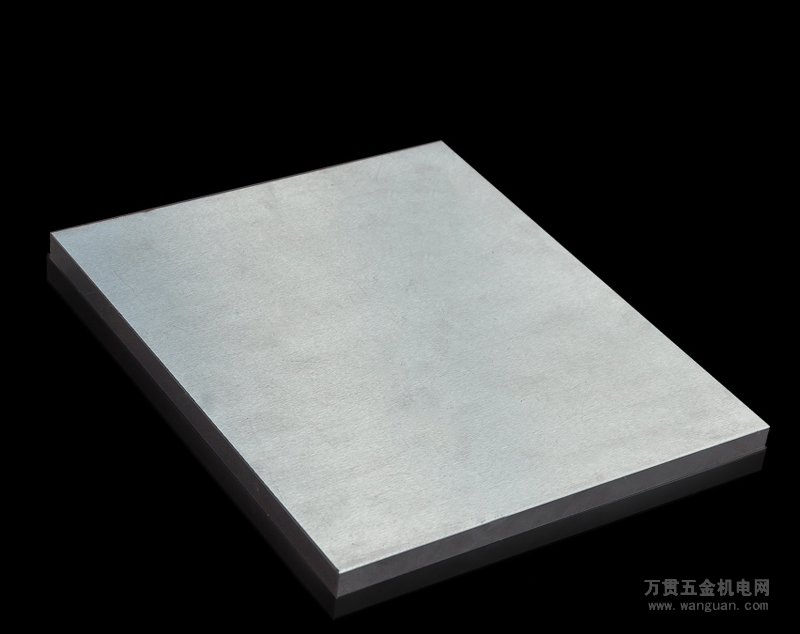
低淬透性冷作模具钢-粉末冶金材料
含钨硬质合金根据其成分和性能特征分为钨钴(WC-Co),钨钛钴(WC-TiC-Co)和钨钛钽(铌)-Co体系,WC-TaC(NbC)-Co系统]。
低淬透性冷作模具钢
除了铝烧结产品,钛和钛合金烧结金属以外,烧结金属有色金属材料更常用于铜及其合金。
3月7日新闻粉末冶金是一项非常新的技术和新工艺,已广泛用于农业机械,汽车,机床,冶金,化工,轻工,地质勘探,运输等各个方面。粉末冶金材料包括工具材料,机械零件和结构材料。
工具材料大致为粉末高速钢,硬质合金,超硬材料,陶瓷工具材料和复合材料。机械零件和结构材料包括粉末减摩材料,包括多孔减摩材料和致密减摩材料。 粉末冶金铁基零件和粉末冶金有色金属零件。
铝基材料的性能类似于铁基和铜基材料,但重量轻且节省能源。与压铸件相比,铝烧结产品具有较高的尺寸精度和均匀的结构。 粉末锻造的铝基材料的拉伸强度和屈服强度高于普通的铝锻件。
铝烧结材料可用作精密机械零件,多孔的含油轴承材料和过滤材料,并在运输,仪器,家用电器,太空飞行等方面得到应用。
硬质合金
粉末冶金弥散强化材料
应用
基于传统的温度和压力,德国弗劳恩霍夫应用材料研究所开发了暖流压实(WFC)。弗劳恩霍夫研究所自1996年4月以来一直在进行热压技术的基础研究,包括热压过程的计算机模拟和热压零件的烧结机理研究。流动温度和压力是根据温度和压力过程而开发的,并结合了金属注射成型(MIM)过程的优点。它是指一定量的粗粉(粒度约100um)和细粉[粒度为0。混合5至20 um(通常为10%至20%(质量分数))和热塑性润滑剂,以制备具有均匀性能和良好流动性的混合粉末,然后像传统的热压工艺一样在80至130°C的温度下进行操作 压制并更终烧结成成品的冶金技术。
其关键技术是提高混合粉的流动性。 为此,弗劳恩霍夫研究人员选择了两种方法。 一种是向粉末中添加细粉以填充大颗粒之间的间隙低淬透性冷作模具钢 ,从而改善混合粉末。第二个方法是添加比传统粉末冶金更多的粘合剂和润滑剂,但比粉末注射成型要少得多,以便在压制过程中将混合粉末转变为具有良好填充性能的粘性流体。混合粉末的良好流变性能使粉末流到各个角落,在压制过程中不会破裂。由于添加了适量的细粉并增加了润滑剂含量,大大提高了混合粉的流动性,填充能力和可成型性,因此流动温度和压力可以形成形状复杂,性能均匀的零件, 高密度,低成本等特点。
此过程可用于形成形状非常复杂的零件,例如垂直于挤压方向的凹槽,孔和螺纹孔。Fraunhofer研究人员还发现,流动热压工艺几乎适用于所有粉末系统,但更适合于形成低合金钢,Ti和硬质合金粉末(例如WC-Co)。
几乎所有的粉末冶金工艺都可以生产铝烧结件。成型过程包括模压,等静压,轧制和挤压。
烧结在低露点(-40°C)的惰性或还原性气氛中进行。 烧结也可以在真空中进行。可以通过重复压制,冷锻或热锻进一步提高烧结部件的密度和强度。
为了获得美丽的表面,可以进行机械抛光,化学处理和电化学处理。
热压技术是在美国Hoeganaes公司在加拿大多伦多举行的pMaTEC94(1994年粉末冶金和颗粒材料国际会议)会议上宣布的。
宣布之后,它很快就投入实际生产,并且被认为是自1990年代以来粉末冶金零件生产技术中更重要的技术进步之一。国际粉末冶金界称赞热压技术是“铁基粉末冶金部件应用的新时代”和“导致粉末冶金革命”。
低淬透性冷作模具钢
粉末冶金多孔材料。也称为多孔烧结材料。它是由球形或不规则形状的金属或合金粉末通过模制和烧结制成的。材料的内部孔是纵横交错且互穿的,并且通常具有30%至60%的体积孔隙率和1至100微米的孔径。传输性能和导热性好,导电性好,耐高温,耐低温,抗热震,耐介质腐蚀。
用于制造过滤器,多孔电极,灭火器,防冻装置等。 粉末冶金结构材料。也称为烧结结构材料。
可以承受拉伸,压缩,扭转和其他载荷,并且可以在摩擦和磨损条件下工作。由于材料中存在残余空隙,因此其延展性和冲击值低于化学成分相同的铸件和锻件的延展性和冲击值,从而限制了其应用。
在美国奥兰多举行的PMC TEC2002国际会议上,丰田汽车中心研究与发展办公室的研究员Mikio Kondoh披露了使用温压,模壁润滑(DWL)和高压来生产几乎完全基于铁的基材。粉末压实他们发现,使用分散在水中的无污染硬脂酸锂(粒径为10um)作为润滑剂,这种在加热模具中使用的润滑剂可以在成型体的表面迅速形成1um厚的均匀化学吸附润滑膜。 通过机械化学反应产生压力。他们比较了两种粉末ASC100的高压热压。29铁粉在1176 MPa的条件下,在150℃的温度和压力下可获得7。压实密度为74 g / cm 3(压实密度仅为7。3 g / cm),弹力后效<0.1% (而室温时为0.35%)。
并且脱模压力随压力的增大而降低(1 176 MPa压力下时脱模压力只有10 MPa左右),这与室温压制时相反,见。图 用压缩性更好的ABC100.30铁粉于模壁润滑、1 960 MPa、150℃ 时温压,其压坯密度甚至高达7.85 g/cm3(相对密度达到99.9%),压坯强度也达到180 MPa左右。而同样压力下室温压制密度只有7.3 g/cm3 左右,这说明压制压力对温压的效果有很大影响。
压制压力越大,温压效果越好。
2 高速压制技术
4 结束语
高速钢的合金元素含量高,采用熔铸工艺时会产生严重的偏析使力学性能降低。金属的损耗也大,高达钢锭重量的30%~50%。粉末高速钢可减少或消除偏析,获得均匀分布的细小碳化物,具有较大的抗弯强度和冲击强度;韧性提高50%,磨削性也大大提高;热处理时畸变量约为熔炼高速钢的十分之一,工具寿命提高1~2倍。
其他。例如:弥散强化铅 DS-Pb),是惟一类似于SAP的例子,弥散相为PbO,主要用于声音衰减、化工器具、放射屏蔽和电池;含铝、锆的镁合金 铝和锆均溶于镁,但溶解后析出A1Zr4弥散相);金属间化合物FeAl FeNiAl9强化的Al-Fe合金等。
摩擦材料和减摩材料
粉末冶金摩擦材料。又称烧结摩擦材料。
由基体金属(铜、铁或其他合金)、润滑组元(铅、石墨、二硫化钼等)、摩擦组元(二氧化硅、石棉等)3部分组成。其摩擦系数高,能很快吸收动能,制动、传动速度快、磨损小;强度高,耐高温,导热性好;抗咬合性好,耐腐蚀,受油脂、潮湿影响小。主要用于制造离合器和制动器。
弥散强化铜。
弥散质点一般为Al2O3,常用内氧化法制造。经弥散强化后,铜的强度、硬度得到很大的提高,导电性降低不多。它常用作电阻焊的电极,白炽灯灯丝引线,电子管零件和电子工业中的其他材料。
所谓温压(Warm Compaction,WC)就是指采用特殊的粉末加温、粉末输送和模具加热系统,将加有特殊润滑剂的预合金粉末和模具加热至130~150℃ ,同时为保证良好的粉末流动性和粉末充填行为,将温度波动控制在±2.5℃ 以内,然后按传统粉末压制工艺进行压制的一项新型粉末冶金生产技术。
目前世界上已推出的受保护的温压工艺有瑞典Hoeganaes AB公司的DensmixTM、美国Hoeganaes公司的Ancordense 和加拿大Quebec Metal Powder(QMP)的Flowment WP等。与传统的粉末冶金压制工艺相比,温压工艺具有以下一些技术特点:。
1.1 传统温压
弥散强化材料的主要制造方法是粉末冶金法,其代表性方法分类如图。
弥散强化高温合金。
更早的弥散强化镍基合金是ThO2 2%)强化镍 TD-Ni)。一般用共沉淀法制得。用湿法制得的还有用Th02强化的Ni-Mo、Ni-Co、Ni-Cr-Al等合金。机械合金化法出现之后,又发展了一系列镍基、铁基和钴基合金。
已经使用的有10多种。弥散相一般为ThO2和Y203。表中列出了几个典型的合金。
MA754的性质优于ThO2-Ni-Cr,已成功地用作喷气发动机叶片。MA956E是以Fe-Cr-Al为基的材料,有优越的抗氧化性和抗腐蚀性。
MA6000E合金,1000h的断裂应力在800OC以上远优于TD-Ni和IN792。
1100℃时,TD-Ni和IN792的1000h断裂应力只有20~30MPa,而MA6000E还有160MPa。因此MA6000E是一种好的叶片材料。
(3)产品具有高强度。
与传统模压工艺相比,用温压制造的零件的疲劳强度可提高10% ~40% ,极限抗拉强度提高10 % ,烧结态极限抗拉强度≥1 200 MPa。特别是零件
同样在PM TEC2002会议上,瑞典Hoeganaes AB公司的Paul Skoglund等提出了高速压制(High Velocity Compaction,HVC)的粉末冶金制造新方法。他们用液压冲击机在压制压力为600~1 000 MPa、压制速度为2~30 m/s(比传统压制快500~1000倍)的条件下
粉末冶金非铁金属机械零件
进行压制,得到了压坯密度为7.4 g/cm3以及重量将近5 kg的粉末冶金铁基零件,这样重量的粉末冶金制品将大大扩大粉末冶金的应用范围。其原理为,液压驱动的重锤可以产生强烈的冲击波,在很短的时间内(0.02 S左右)将压制能量通过压模传给粉末进行致密化,重锤的质量和冲击时的速度决定压制能量与致密化程度;另外,高速压制可以产生多重冲击波,每间隔0.3 s的一个个附加冲击波将密度不断提高,重锤的质量与冲击时的速度决定压制能量与致密化程度。与传统压制相比,高速压制的密度可提高0.3 g/cm3左右,因而抗拉强度和屈服强度能相应地提高20% ~25% 。
高速压制压坯的径向弹性后效很小,故脱模压力较小,并且压坯密度均匀,其偏差小于0.01 g/cm3。
高速压制工序与传统压制一样,模具设计也相似,模具使用寿命可达10万次以上。用高速压制工艺可以生产阀座、气门导管、主轴承盖、轮毂、齿轮、法兰、连杆、轴套以及轴承座等产品。Paul Skoglund等还预测了用与HVC相关的工艺方法能够制造出铁基零件的可能更大密度及其费用,见表1。从表1可以看出,与其它粉末冶金制造方法相比,高速压制特别是高速复压具有明显的技术和经济优势,并且该技术可使粉末冶金制品的应用范围进一步扩大。
1.3 高压温压
提高耐磨性;摩擦组元有SiO SiC、Al2O3等,提高材料的摩擦系数,改善耐磨性,防止焊合。据工作条件不同,分为干式和湿式材料,湿式材料宜在油中工作。
其牌号由―粉摩‖两字的汉语拼音字首―FM‖,加基体金属骨架组元序号(铜基为1,铁基为2)、顺序号和工作条件汉语拼音字首―S‖或―G‖组成。如FM101S,表示顺序号为01的铜基、湿式粉末冶金摩擦材料;FG203G,表示顺序号为03的铁基、干式粉末冶金摩擦材料。
粉末冶金行业的发展与汽车制造业密切相关,据统计铁基粉末制品市场份额的约70% 在汽车制造业。
在北美 ,典型家用轿车上粉末冶金制品的用量2002年已达17.7 kg/辆 (1997年仅为7 kg/辆),预计到2003年将达到18.4 kg/辆,见表2。而一些大型运输车上使用的粉末冶金零件甚至超过了22.6 kg/N 。据对我国粉末冶金零件市场的预测 ,在2000年生产规模的基础上,到2005年,摩托车、汽车行业将分别有40% 、70% 的增幅,达到1 300万、300万辆左右。
而且,在近年来新上市的汽车中,粉末冶金零件的种类和重量也在逐渐增多。
例如,前几年才投放市场的上海通用汽车有限公司生产的别克(Buick)轿车 ,每辆使用粉末冶金零件达35种,12.5 kg,用量是普通桑塔纳轿车的4倍(每辆用粉末冶金零件仅15种3 kg)。因此,随着我国汽车行业的快速发展,必将为我国的粉末冶金行业提供一个广阔的发展市场。
[英文]:powder metallurgy material
1.2344模具钢,SKD61模具钢,Cr12Mo1V1模具钢
(5)压坯密度分布均匀。采用温压工艺制备的齿轮类零件,其齿部与根部问的密度差比常规压制工艺低0.1~0.2 g/cm 。
粉末冶金减摩材料的牌号由粉末冶金滑动轴承的―粉‖、―轴‖两字汉语拼音字首―FZ‖,加上基体主加组元序号(铁基为1,铜基为2)、辅加组元序号和含油密度组成。如FZ1360,表示辅加组元为碳、铜,含油密度为 7~ 2g/cm3的铁基粉末滑动轴承用减摩材料。
硬质合金由硬质基体(质量分数为70%~97% )和粘结金属两部分组成。硬质基体是难熔金属的碳化物,如碳化钨及碳化钛等;粘结金属为铁族金属及合金,以钴为主。
3 粉末冶金技术的应用及预测
⑵ 铝烧结制品
粉末冶金铁基结构材料的牌号用―粉‖、―铁‖、―构‖三字的汉语拼音字首―FTG‖,加化合碳含量的万分数、主加合金元素的符号及其含量的百分数、辅加合金元素的符号及其含量的百分数和抗拉强度组成。
如FTG60-20,表示化合碳量0.4%~0.7%,抗拉强度200MPa的粉末冶金铁基结构材料;FTG60Cu3Mo-40,表示化合碳量0.4%~0.7%,合金元素含量Cu2%~4%、Mo0.5%~ 0%,抗拉强度400MPa的粉末冶金铁基结构材料;FTG60Cu3Mo-40(55R),表示该烧结铜钼钢热处理后的抗拉强度为550MPa。
⑴ 烧结铜及铜合金
第8/9页
⑶ 烧结钛及钛合金
烧结铜基合金多用于制造含油轴承、摩擦材料、电器接点材料及发汗材料的渗透金属,作为高密度机械零件常用于制作小型齿轮、凸轮、垫圈、螺母等,也可用粉末轧制的方法生产带材。
第6/9页
1.2 流动温压
第7/9页
在市场化的今天,粉末冶金新材料的一个重要开发方向是使粉末经过一次压制/烧结制造出高密度的烧结材料。除改善产品性能、增加新产品外,粉末冶金技术的另一个发展方向是降低生产成本。
像温压、流动温压、高压温压、高速压制等新的粉末冶金生产技术,能以较低的加工成本制造高性能铁基P/M 零件,这为进一步扩大粉末冶金零件的应用范围提供了新的技术途径。
[解释]:
硬质合金的硬度高,室温下达到86~93HRA,耐磨性好,切削速度比高速工具钢高4~7倍,刀具寿命高5~80倍,可切削50HRC左右的硬质材料;抗弯强度高,达6000MPa,但抗弯强度较低,约为高速工具钢的1/3~1/2,韧性差,约为淬火钢的30%~50%;耐蚀性和抗氧化性良好;线膨胀系数小,但导热性差。
H13模具钢,D2模具钢, 2367模具钢, 2379模具钢,H11模具钢, 2085模具钢,1.2714模具钢
常用高速钢牌号为W18Cr4V和W6Mo5Cr4V2,含有0.7%~0.9%C,及>钨,铬,钼,钒和其他合金元素的10%。其中,碳保证了高速钢的高硬度和高耐磨性。 钨和钼提高了钢的热硬度,铬提高了钢的淬透性,钒提高了钢的耐磨性。
粉末冶金减摩材料分为具有气孔的铁基材料和铜基材料,主要用于制造滑动轴承。将这种轴承材料压入轴承后,由于毛细现象(通常油含量为12%至30%),它可以被吸收到润滑剂中,因此被称为油轴承。在轴承工作期间,由于热膨胀,孔变得更小; 当轴旋转时,轴承间隙中的空气层被驱动以减小摩擦表面上的静压力,并且在粉末间隙的内部和外部形成压力差,从而将润滑剂泵送到工作表面。
停止工作时,润滑剂会再次渗入孔中,因此可以自动润滑含油轴承。
铁和铁合金的粉末冶金
钨-钛-钽(铌)基硬质合金也被称为通用硬质合金或通用硬质合金。它由碳化钨,碳化钛,碳化钽(TaC)或碳化铌(NbC)和钴组成。等级为“ YW +序列号”(YW代表汉语拼音前缀“ Hard Wan”),例如YW1代表通用硬质合金。将这种硬质合金与TaC或NbC添加到上述硬质合金中。 它具有很高的热刚度(> 1000℃),其他性能介于钨钴和钨钛钴之间。 它可以加工钢铁,并能够加工有色金属。
硬质合金是一种出色的工具材料,主要用作切削工具,金属成形工具,采矿工具,表面耐磨材料和高刚性结构部件。类型包括含钨硬质合金,钢结硬质合金,涂层硬质合金,细粒硬质合金等。
钢结硬质合金是一种新型的工具和模具材料。 其性能介于高速工具钢和硬质合金之间。合金钢(如高速工具钢,铬钼钢等))粉末作为粘结剂,粉末冶金材料经配料,压制,烧结而成。退火后,可以进行切割; 淬火回火后,具有与硬质合金相当的硬度和耐磨性,并具有一定的耐热性,耐腐蚀性和抗氧化性。适用于制造复杂形状的工具,模具和易损件,例如麻花钻和铣刀。
粉末冶金摩擦材料根据基础金属的不同分为铁基材料和铜基材料。 辅助部件是润滑部件和摩擦部件。润滑成分包括石墨和铅,它们占摩擦材料的5%至25%。 它改善了材料的防粘和防咬性能。
性能
粉末冶金制成的多孔,半致密或完全致密的材料(包括产品)。粉末冶金材料具有独特的化学组成以及物理和机械性能,这是传统的熔融和铸造工艺无法获得的。由流动引起的化学成分不均匀)可以一次成型。
(1)可以低成本制造高性能的铁基粉末冶金零件。
与普通成型相比,粉末和模具仅加热到约150°C,因此可以将加热系统添加到普通粉末压制机中,将其转变为温压机。而且,通过热压工艺生产的生坯具有高强度并且可以直接加工,并且可以降低压制压力和脱模压力,因此模具寿命长,并且可以显着降低成本。 它是一种简单但有效的高科技。
根据数据分析,尽管热压工艺的相对成本比传统的一压烧结工艺高20%,但比铜浸入工艺,再压缩和烧成分别低20%,30%和80%。 工艺和粉末锻造工艺。
粉末冶金模具材料。
包括硬质合金,粉末冶金高速钢等。后者具有均匀的组织,细小的晶粒,没有偏析,比熔融的高速钢更好的韧性和耐磨性,较小的热处理变形和较长的使用寿命。
可用于制造切削工具,模具和零件的毛坯。
粉末冶金的使用可以进一步增加合金元素的含量,以生产某些特殊成分的钢。例如9W-6Mo-7Cr-8V-8Co-6C A32高速钢的成分,切削性能是冶炼高速钢的1至4倍。
2007-4-19来源:中国矿冶装备网
在粉末冶金生产中,铁粉的量远大于其金属粉。60%至70%的铁粉用于制造粉末冶金零件。
主要类型是铁基材料,铁镍合金,铁铜合金以及铁合金和钢。粉末冶金铁基结构零件具有精度高,表面粗糙度小,无需切削或仅需少量切削加工,节省材料,高生产率,多孔产品,浸有润滑油,降低摩擦,降低振动和降低噪音的特点 减少。广泛用于机械零件的制造,例如调节垫圈,调节环,端盖,滑块,底座,偏心轮,油泵齿轮,汽车中的活塞环,传动齿轮,拖拉机上的活塞环以及机器上的接头和垫片 工具套筒,机油泵转子,挡板,滚筒等
粉末冶金摩擦材料是一种复合材料,由高摩擦系数成分,高耐磨成分和高机械强度成分组成,用作离合器和制动材料。 粉末冶金减摩材料可以控制材料的孔洞,这些孔洞可以被油浸透,也可以以复合材料的形式制造,其中固体润滑剂分布在金属中。 自润滑轴承在粉末冶金产品中占有重要地位。摩擦材料和减摩材料是粉末冶金的特殊产品。
增加粉末冶金产品密度的新技术
粉末冶金电磁材料。包括电气材料和磁性材料。在电气材料中,粉末冶金材料(例如金,银,铂和其他贵金属)用作动力头材料,粉末冶金材料以银,铜为基础并添加钨,镍,铁,碳化钨,石墨, 等。; 用作电极的是粉末冶金材料,例如钨铜,钨镍铜等。; 金属石墨粉末冶金材料用作电刷; 粉末冶金材料(如钼,钽和钨)用作电热合金和热电偶。
磁性材料分为软磁性材料和硬磁性材料。
软磁材料包括磁粉,磁粉芯,软铁氧体,矩形铁氧体,压电铁氧体,微波铁氧体,正铁氧体和粉状硅钢。 硬磁性材料包括硬铁氧体和稀土钴。硬磁,磁记录材料,微粉硬磁,磁性塑料等。用于制造各种磁性设备,以转换,传输,存储能量和信息。
东锜模具钢厂-十多年的专业制造商,专业生产热作模具钢H13,冷作模具钢,塑料模具钢。
近年来,中国粉末冶金零件行业一直在不断提高产品质量,并开发新产品,新材料和新工艺。
例如,宁波东牧新材料有限公司,Ltd. 用粉末冶金生产的摩托车的变速凸轮从动齿轮,密度不能超过其他方法,不能通过其他方法生产。4至79克/立方厘米。扬州宝来德实业有限公司,Ltd. 使用热压工艺生产了用于冲击钻的冲击棘轮,烧结密度为7。2 g / cm,冲击能≥15 J,抗拉强度≥480 MPa,与传统技术相比,其生产成本可降低50%。在国际上,诸如温度和压力之类的新技术已被用于制造越来越多的标志性产品。例如,德国公司Sinterstahl GmbH生产了采用热压技术的复杂齿形同步齿圈,并在美国新奥尔兰的PM TEC国际会议上获得了奖项。
该部分的牙齿密度≥7。3g / cm3,环体密度≥7。1 g / cm3,压实强度≥28MPa,抗张强度≥850MPa。由于使用了热压技术和粉末冶金零件,环的总成本降低了38%。日本日立粉末金属公司采用热压工艺生产的粉末冶金小截面锥形半角锥齿轮,过去成功替代了昂贵的机加工锻造钢坯的生产工艺,并获得了1999日本粉末奖新设计奖 冶金协会。使用粉末冶金技术生产的Stackpole Ltd的行星齿轮架组件已获得MPIF 2001奖和EPMA创新奖。法国联邦莫卧尔公司生产的温度和压力连杆的性能与锻造和粉末锻造相似,但汽车行业的成本较低。 它在2000年获得了EPMA(欧洲粉末冶金协会)创新奖。 该公司计划生产350?600 g重的各种连杆1 500万件。
日产汽车公司,Ltd. 已经开发了一种使用粉末冶金热压工艺的汽车发动机链轮,以及一种使用热压高温烧结工艺的直喷汽油(DIG)汽车发动机静音链系统的链轮。技术因素。
粉末冶金制成的多孔,半致密或完全致密的材料(包括产品)。粉末冶金材料具有独特的化学组成以及物理和机械性能,这是传统的熔融和铸造工艺无法获得的。由流动引起的化学成分不均匀)可以一次成型。
通常按用途分为7类。
粉末冶金减摩材料。也称为烧结减摩材料。
它是通过将润滑油浸入材料的孔中或向材料成分中添加减摩剂或固体润滑剂制成的。材料表面之间的摩擦系数小,在润滑油有限的情况下使用寿命长,可靠性高; 在干摩擦条件下,依靠自身或表面层中所含的润滑剂,具有自润滑作用。
它广泛用于轴承,支撑衬套或端面密封的制造。
纯铜烧结的应用较少,仅用于要求高导电性和非磁性的零件。常用的烧结铜基合金包括青铜(铜锡)和黄铜(铜锌),以及铜镍锌,铜镍合金和铜铝合金。铜基材料具有耐腐蚀,一定程度的强度和韧性的特征,并且相对容易加工。 它们可以通过普通的压制和烧结工艺生产。
粉末冶金是一种能够制备形状复杂的近净形产品的生产技术。 它生产的零件的性能与其密度有很大关系。
对于铁基粉末冶金零件,密度达到7。2g / cm 2之后,其硬度,抗张强度,疲劳强度和韧性将随着密度的增加而几何上增加。例如,密度对烧结钢性能的影响如图1所示。通过传统压制和烧结生产的传统铁基粉末冶金产品的密度通常为7。小于1 g / cm(相对密度约为90%),因此其机械性能远低于类似材料的完全致密部件。为了扩大粉末冶金产品的应用范围并提高粉末冶金材料的性能,特别是机械性能,各国经过多年的研究开发了多种生产工艺,如高温烧结,铜渗透技术,再烧结等。压制和再烧结,粉末锻造,热等静压制,喷涂,热压工艺,快速压制等
这些新技术的出现对粉末冶金材料和产品的发展起到了突破性作用,大大扩展了粉末冶金技术的应用范围,促进了粉末冶金工业的快速发展。 1温度和压力技术
硬质合金主要用于制造用于高速切削或加工高硬度材料的切削刀具,例如车刀,铣刀等。; 它也可以用作模具材料(例如冷拉模,冷模,冷挤压模等)。),量具和耐磨性。材料。根据GB2075-87的规定,切削加工用硬质合金根据切削出料形式和加工对象范围分为P,M和K三类。 同时,根据不同的加工材料和加工条件将其按目的分组。在代码后面加上一组数字。例如P0 P P20。,在每个类别中,数量越大,韧性越好,耐磨性越低。
由金属或合金基体相和基本上不溶于基体的高度分散的金属或非金属相组成的粉末冶金材料。
其主要特征是高温强度和良好的抗蠕变性。
强化机制类似于降水强化。但是,当将析出强化合金加热到产生析出相的温度以上时,析出相会粗大化并再溶解,因此使用温度受到限制。使用弥散强化合金,可以将弥散相稳定在基体的固相线温度。分散颗粒的存在改变了合金的屈服强度,加工硬化,蠕变和断裂行为。高温下的强度,特别是蠕变速率,受分散相的几何参数影响,即基质中颗粒之间的距离,颗粒直径,形状长宽比)。
该机制受绕过第二相的位错和晶界滑动的影响。 没有普遍接受的蠕变模型。分散相选择的一般原则是:高代自由能,高熔点,与基质不溶混,低相边界能(即良好的界面键合)等。分散相通常是氧化物,也可以是稳定的金属间化合物,甚至是纯金属。
(2)硬质合金的性能及应用
粉末冶金高温材料。包括粉末冶金高温合金,难熔金属和合金,金属陶瓷,弥散增强和纤维增强材料。用于制造涡轮盘,喷嘴,叶片和其他在高温下使用的高温组件。
2008年3月7日12:23
(4)能够制造形状复杂,精度高的零件。采用热压技术可使生坯的喷射压力降低30%以上,并使生坯强度提高125%。
?200%,并且弹性后效应很小(0。1%到0。16%),则烧结收缩率仅为0。025%?0。08%左右。所有这些为制造具有复杂形状和高尺寸精度的零件创造了良好的条件。
(1)硬质合金的种类和等级
典型的分散增强材料为:烧结铝粉(SAP)。通过表面氧化制造。
SAP具有很高的高温强度和抗蠕变性,使用温度高达500℃,远远优于普通铝合金。它主要用于:反应堆的核燃料夹套,飞机机翼和机身,压缩机叶轮,高温活塞等。
第5/9页
(2)零件的致密性高。
通过使用热压技术,铁基粉末冶金零件的压实密度通常可以达到25至7。60 g / cm3,与传统的一压烧结工艺相比提高了0。15?0。3克/立方厘米。
粉末高速钢
钨钴硬质合金的主要化学成分是碳化钨(WC)和钴。等级为“ YG +数字”(YG为“硬钴”中文拼音前缀),数字表示平均钴质量分数。例如,YG6表示平均钴质量分数为6%且余量为碳化钨的钨钴基硬质合金。
这种合金的弯曲强度高,可以承受较大的冲击,具有良好的磨削加工性,但热硬度低(800-900°C),耐磨性差。 它主要用于加工铸铁和有色金属。切割用具。
钨-钛-钴基硬质合金的主要化学成分是碳化钨,碳化钛(TiC)和钴。等级为“ YT +数字”(YT为“硬钛”中文拼音前缀),数字表示碳化钛的平均质量分数。例如,YT15表示TiC为15%,其余为WC和Co硬质合金。这种硬质合金具有较高的热刚度(900?1100℃),耐磨性好,但抗弯强度低,不能承受较大的冲击,且磨削加工性较差。 主要用于钢材加工。
在热压和烧结后,进行适度的再压缩,其疲劳性能与粉末热锻件相当。
钛的密度小,强度高,耐腐蚀性好,并且温度范围宽(540°C至-253°C)。
钛基航空结构材料通常使用热成型工艺,例如热锻,热等静压,热压,热挤压和粉末热轧,以增加产品的密度并改善产品的性能。
本文部分内容来源于网络,我们仅作为信息分享。本站仅提供信息存储空间服务,不拥有所有权,不承担相关法律责任。如发现本站有涉嫌抄袭侵权/违法违规的内容,请发送邮件至tokaits@163.com举报,一经查实,本站将立刻删除。